我窥探了英特尔最大的离岸工厂 | ENBLE
我窥探了英特尔最大的离岸工厂 | ENBLE

很少见到科技巨头向外界展示其真实运作方式。但这正是英特尔邀请全球媒体代表和媒体记者参观其马来西亚工厂时的初衷。作为其2023年科技之旅活动的一部分,这家芯片制造商向我们详细介绍了CPU的制造过程。我学到了很多知识,在分享我的经验之前,先来简要了解一下该公司在马来西亚的历史和未来计划。
英特尔于1972年在马来西亚建立了第一家离岸设施,当时有100名员工。如今,位于槟城和库里姆的两个主要设施占地近900,000平方英尺,拥有15,000名员工。

随着需求的增长以及为了跟上其IDM 2.0战略,英特尔已经在扩大其设施的覆盖范围。一座名为Pelican的新先进封装设施和一座名为Falcon的组装测试设施目前正在建设中,预计将在未来两年投入运营。该公司还计划在未来建造总面积达700万平方英尺、超过200万平方英尺制造空间的16栋建筑物。
参观英特尔马来西亚
参观活动分为两天,我们首先参观了槟城组装和测试(PGAT)设施。这是硅芯片组装、验证和错误测试的地方。而库里姆设施则是魔法的起点。英特尔库里姆切割准备设施(KMDSDP)是一座先进的处理硅晶圆的设施,硅晶圆是构成最佳处理器的原材料。
该工厂接收来自制造工厂的硅晶圆,进行切割准备工艺,并随后将其分类放置,以便在世界各地的英特尔组装/测试设施进行封装和测试。与槟城设施位于岛上不同,KMDSDP设施位于大陆上,这意味着需要乘坐一辆更长的巴士穿越一个美丽的海上桥梁。

一旦我们到达库里姆,我们接受了简要介绍,并被要求穿戴特殊的兔子服,还有额外的头套和胡须保护,然后才能进入。这是必要的,因为制造区域需要无尘。当然,这也意味着我们不允许携带包括手机、相机或其他记录设备在内的任何物品。
准备切割、分类切割

KMDSDP设施负责两个主要操作 – 切割准备和分类切割。在切割准备阶段,完整的300mm晶圆从制造设施接收,并粘贴到柔性的mylar上。这些是半透明的片材,必要时可确保每个芯片在切割和分离后仍保持在其位置上。
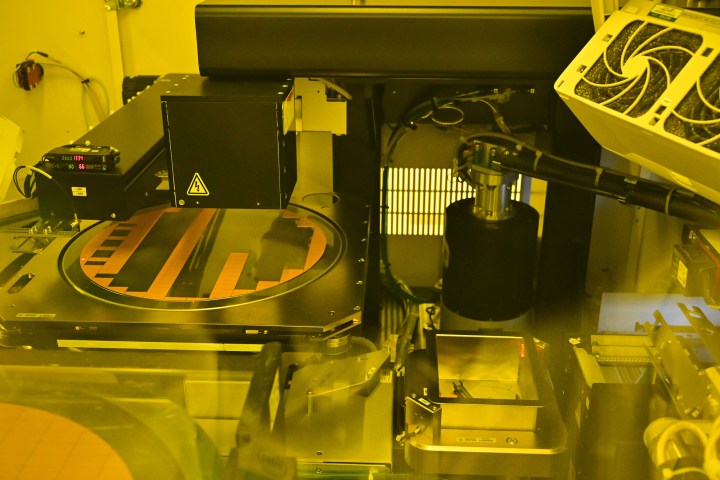
根据处理器的类型,这些晶圆片经过多道工序,包括研磨、激光划线和机械切割,来制造单个芯片。接下来,使用特殊的真空和紫外线组合,将芯片从mylar上分离出来。这些单个芯片然后使用机械臂放置到托盘中,并放入较大的塑料盒中,然后运送到后续的分类操作中。
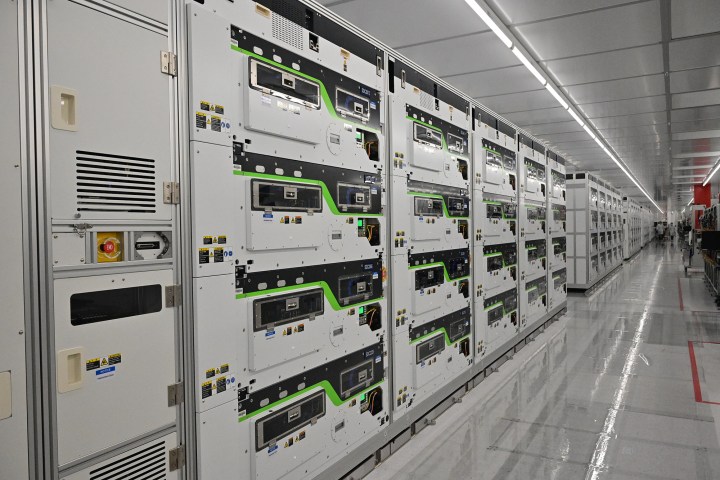
接下来,这些芯片都要经过检测以确定是否有缺陷,并同时进行分类。为了完成这个任务,英特尔使用了大型的分类模块,它们像巴士一样大,共有20个单独的测试单元。每个测试单元重约1000磅,为了操纵它们,有一种专门设计的升降机构,它像气垫船一样悬浮在地板上使用空气垫。只用一只手就可以移动这个巨大的运输工具,感觉几乎像是魔法。
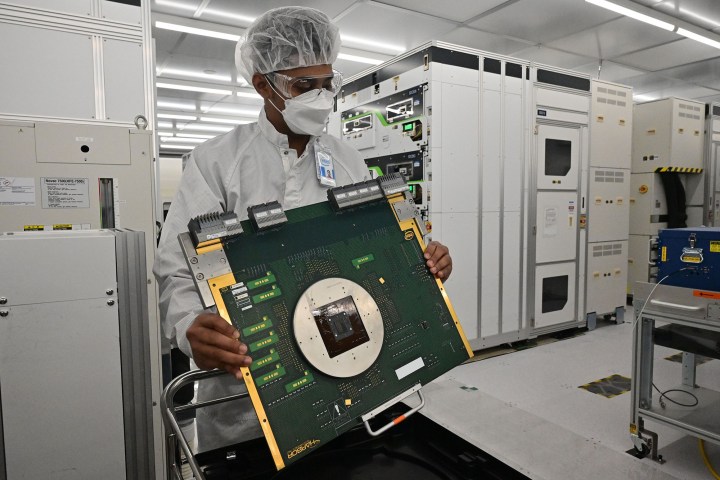
托盘从一端装载,然后分配到各个测试单元。由于每个测试单元都可以独立运行,工作人员可以从分类模块中的一个测试单元进行维护。每个芯片都使用配备数千根细针的探针卡进行测试,这些细针比人的头发还细,连接到测试设备内的集成电路上。这个探针卡测量芯片电路的电特性,以评估可靠性并识别缺陷。所有的测试都是自动完成的,而工作人员则使用各种监视器观察整个过程。

还有一些特殊的自动引导车(AGVs)吸引了大家的注意,主要是因为它们像冰淇淋车一样发出声音。它们的主要任务是处理存储空间和测试设备之间的批次移动。它们几乎不需要人工干预,在专用路径上在设施周围悬浮移动。
一旦一个托盘完成了测试和特性化阶段,它们就会被送回到将晶圆切割成单个芯片的区域。未通过测试阶段的芯片会被单独收集,然后被丢弃或回收。通过了所有测试的芯片所在的托盘会被分类并分配给特定的SKU(Core i9, Core i7等)。每个芯片都会从托盘中取出,封装在两层薄膜之间,然后卷成卷筒,以便运输到全球各地的装配和测试设施进行进一步处理。

进行组装和测试
接下来的参观部分包括参观位于槟城岛上的槟城装配和测试(PGAT)设施。这个制造设施每天都会组装和测试数以百万计的各种芯片。基本上,所有的卷筒都会被送到这个设施,然后每个芯片都会被取下、封装和测试,然后才能准备好上市。

在PGAT的组装和测试过程中,有六个关键阶段。首先是芯片焊接过程,将芯片与基板(CPU的基础材料)焊接在一起。这是使用先进的面对面(F2F)芯片对芯片焊接技术进行的,该技术首次在2019年引入。该过程需要高度精确度,因为任何缺陷都会对芯片造成严重损坏。在芯片和基板之间均匀涂上一层环氧树脂填充物,以消除微观间隙。
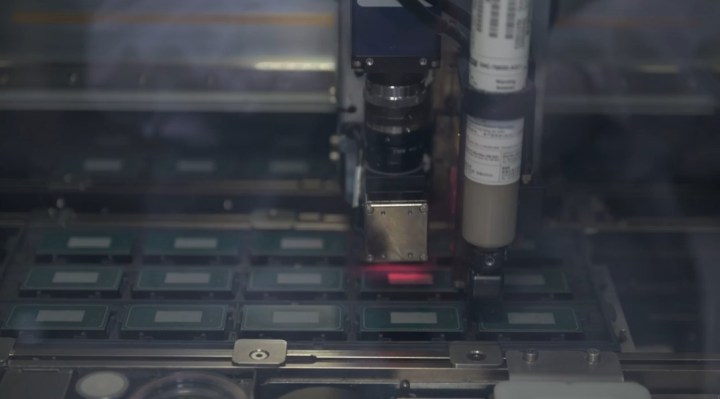
下一步是将集成散热盖(IHS)或CPU的盖子固定在上面。这有助于在最终用户系统中有效散热。首先使用一台机器在芯片上涂上一定量的热界面材料,然后涂上粘合剂,以便将IHS盖子放在适当位置。现在我们有了一个成品,准备投入使用。但在此之前,它必须经过一些严格的测试。
一旦CPU准备好了,它必须经过各种测试以确保产品按预期工作。这是在槟城PG16的设计与开发实验室完成的。
首先是烧入测试,Intel会将芯片暴露在高温和高电压下,以识别和消除任何缺陷。成功通过此测试的芯片将继续进行电气测试,包括测试所有电气路径以及功能。最后,芯片必须经过PPV测试阶段,以验证平台产品在运行Windows、Linux或其他操作系统环境的实际客户计算机系统中的功能。本质上,它是一个模拟客户环境的过程,并且还会测试内存、PCIe通道等各个方面。
参观的最后阶段包括参观系统集成和制造服务(SIMS),这是一个特殊的工厂,用于在生产过程中测试和验证CPU的设备。这个设施不仅为Intel马来西亚制造测试设备,还将它们运送到世界各地的其他Intel设施。

我们有机会查看一些测试设备,包括高密度烧入(HDBI)测试设备、高密度模块化测试(HDMT)测试设备和系统级测试(SLT)设备。HDBI测试设备用于在Intel CPU上执行高温和高电压的烧入应力测试,而HDMT提供了执行类或后端测试的能力。Intel表示,这个测试设备在他们的工厂和实验室中用于新产品开发和CPU生产。最后,SLT用于确认Intel产品在类似客户环境中的功能。每个测试设备都设计与CPU的特性和精确要求相符,确保足够的测试覆盖率并维持产品质量。
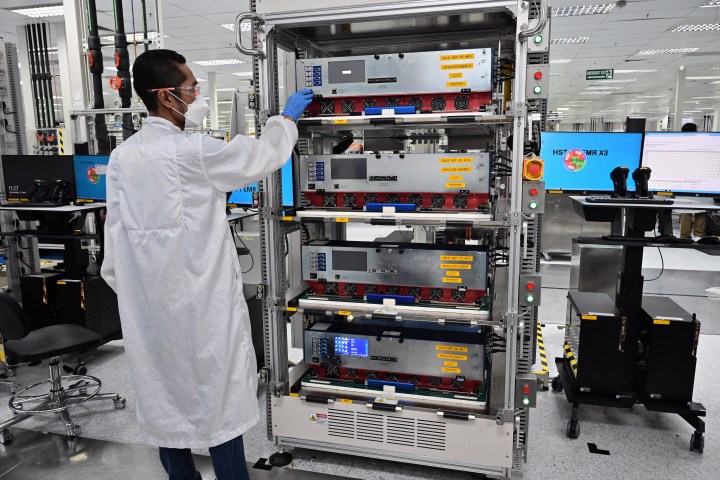
前所未有的体验
目睹和理解CPU制造过程的整个经历确实是独一无二的。我对运作规模之庞大和生产单个最终产品所涉及的复杂性印象深刻。整个制造设施就像一个运转良好的机器,但它是由公司员工的各种复杂性和不懈奉献所支撑。
在制造设施的各个部门中穿行不仅让我更深入地了解了公司如何打造其顶级芯片,还清晰地展示了Intel的未来。该公司在未来四年内引入五个节点的承诺可能看起来是一种营销策略,但考虑到其制造工厂的令人印象深刻的能力,这似乎完全可行。这些工厂还确保公司在制造、创新和产品领导力方面符合其IDM 2.0战略。
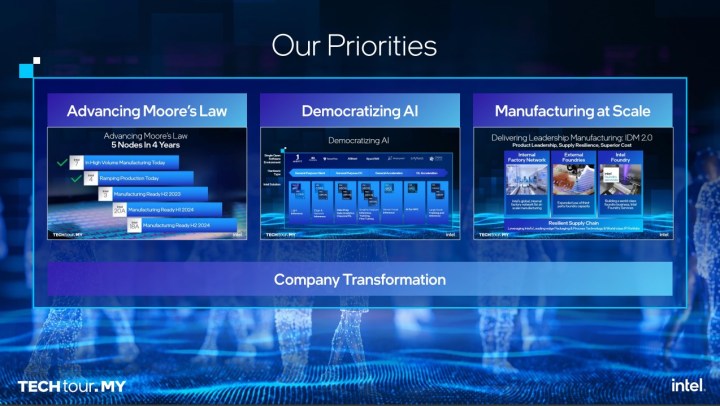
然而,重要的是要认识到Intel不会在成功的道路上一帆风顺。来自竞争对手如AMD和其他芯片制造商的激烈竞争,只有时间才能揭示Team Blue能否在行业中保持领先地位。
目前,我们预计Intel将在今年晚些时候推出以第14代“Meteor Lake”为名的新移动芯片组。预计这将是该公司的重要里程碑,因为它将采用Intel 4工艺,使其成为首个采用7nm工艺的芯片系列。此后,有传言称下一代台式机处理器也将作为对现有第13代Raptor Lake系列的刷新而到来。